内容纲要:
• 结晶工艺开发目的
• 结晶工艺开发流程图
• 结晶溶剂选择
• 成核与生长
• 过饱和度释放控制
• 纯度控制
• 晶体形貌(形状)控制
• 结晶方式选择
• 结晶工艺开发常见问题
前言
在制药工业中,超过大半的药物以晶体形式存在,85% 以上的生产过程中都含有结晶操作。90% 以上的制剂产品的 API 是晶体形态;相比于无定形,晶体形态总体上化学稳定性和物理稳定性更优。
结晶过程使原料药具有特定的纯度、粒度及晶型,结晶工艺直接影响原料药加工与制剂生产,对于大分子、难溶性药物晶体生长速度慢,常用手段难以拿到合格产品,需针对性开发工艺;对于溶解性特别好的药物,产品容易油析,难以固化,同样需针对性开发工艺。
基于此,特撰写本结晶工艺开发流程。
结晶工艺开发目的
原料药生产过程中通常会对中间体或 API 进行结晶操作来达到如下目的:
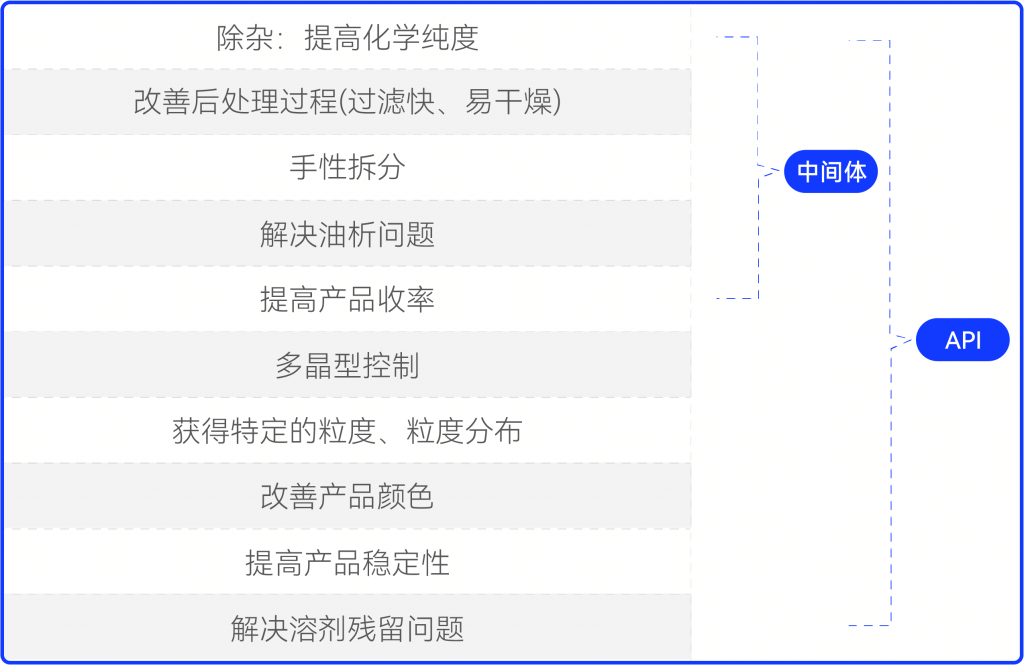
结晶工艺开发流程图
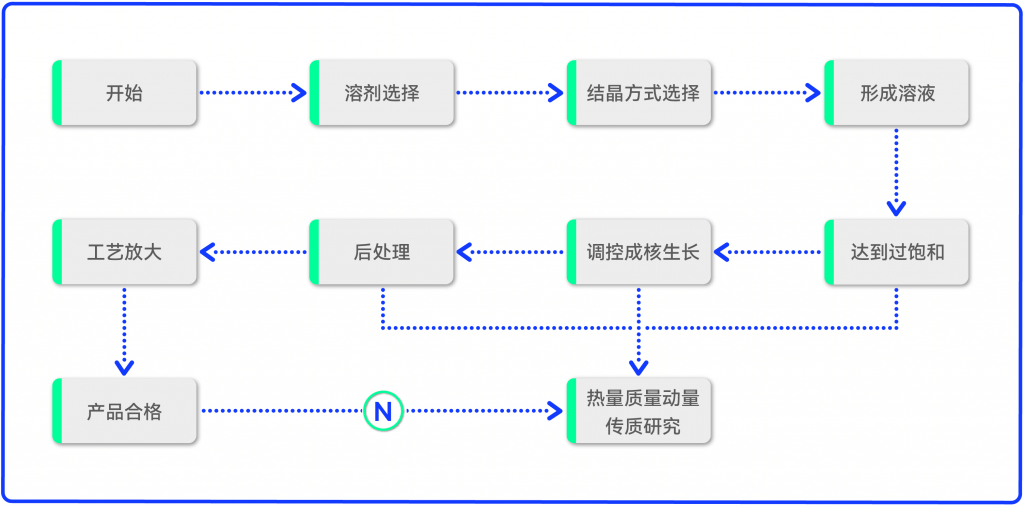
结晶溶剂选择
溶剂的选择对 API 结晶工艺开发至关重要,对产品的纯度、晶型、形貌(颗粒属性)、收率等皆有重大影响。在选择溶剂时,应规避以下几个问题:
• 忽视溶剂的安全性、毒性——忽视制药过程中的合规化需求,使用一类/二类溶剂或其它特殊溶剂,导致溶残不可控、安全性降低等。
• 使用大倍率溶剂,导致收率偏低、设备处理量不足、成本增加。
• 忽视除杂能力——所用溶剂应对 API 与杂质的溶解度具有较大差异性,通常基于相似相溶原则筛选溶剂。
• 未考察溶液热稳定性,导致放大生产过程中产品降解。
• 忽视对晶型的影响——溶剂化物、溶剂底物模板效应:特定的溶剂倾向制备特定的晶型;溶剂-溶质相互作用对成核、晶体生长的控制以及溶剂介导的多晶型转变;避免使用会产生溶剂合物的溶剂。
• 晶习控制——由于溶剂粘度、表面张力等对结晶动力学的影响,不同溶剂可能会形成不同晶习,同一晶型不同晶习可能带来不同的粒度,进而影响粒度分布。
成核与生长
结晶工艺开发的核心就是调控成核与生长,成核是新晶核的诞生,是少量离子、原子或分子以结晶固体的形式排列形成晶核的过程,包括从溶液中自发的初级成核还是在现有晶体的存在下的次级成核。
一旦实现成核,晶体生长将占结晶过程的主导地位,晶体生长是引导晶核生长为具有特定尺寸和形状的晶体的过程。此过程中,固体分子中的晶格结构、溶剂选择和晶体生长过程中的添加剂等都是影响晶体形状的关键因素。
过饱和度释放控制
下图为结晶最常见的结晶相图:
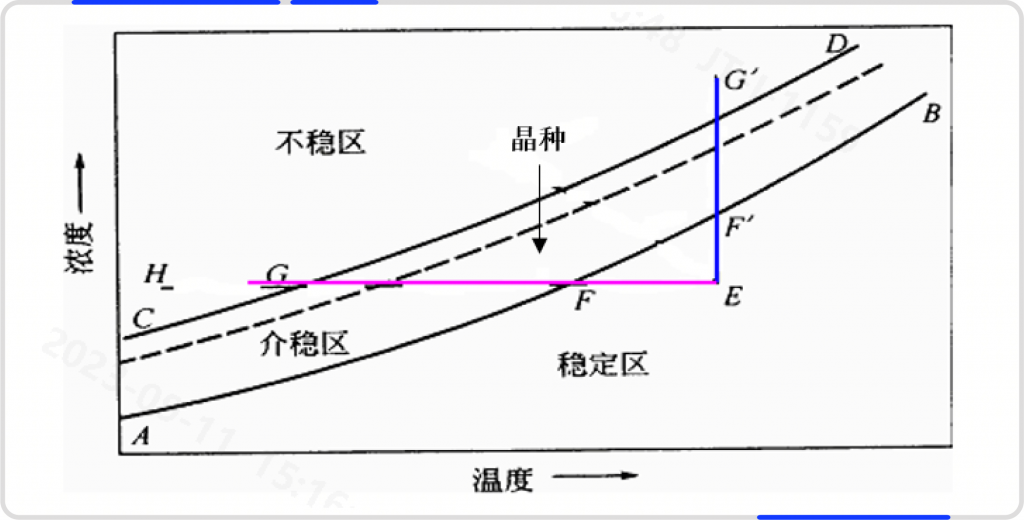
其中AB为溶解度曲线,CD为超溶解度曲线
在溶解度曲线下方为稳定区,不会有固体析出;在超溶解度曲线上方为自发成核不稳定区,为无法控制区域。因此结晶参数要控制在两条曲线之间,两条曲线之间的区域通常被称作介稳区。
结晶参数靠近溶解度曲线时,会产生大颗粒晶体,缺点是过饱和度释放慢,会延长工艺所用时间。
结晶参数靠近超溶解度曲线时,过饱和度释放快,容易得到小颗粒晶体。
结晶工艺开发的核心就是调控过饱和度的释放,来生产符合要求的合格产品。
纯度控制
晶体本身的纯度很高,其杂质主要是由于晶体包裹和表面粘接母液而造成的,通过夹杂或黏附到母液中的杂质,可以通过改变生长条件(即结晶条件或下游工序的加工条件)来控制,如增大产品粒度,减少粒度分布宽度,控制晶体形状等方式都可带来更好的固液分离,从而降低夹杂或黏附到母液,通过分离结晶技术可以获得更高的纯度。通过形成部分固溶体或完全固溶体而将杂质引入晶格的过程不受工艺条件的影响,通常只能通过反复重结晶等手段来实现纯化效果。
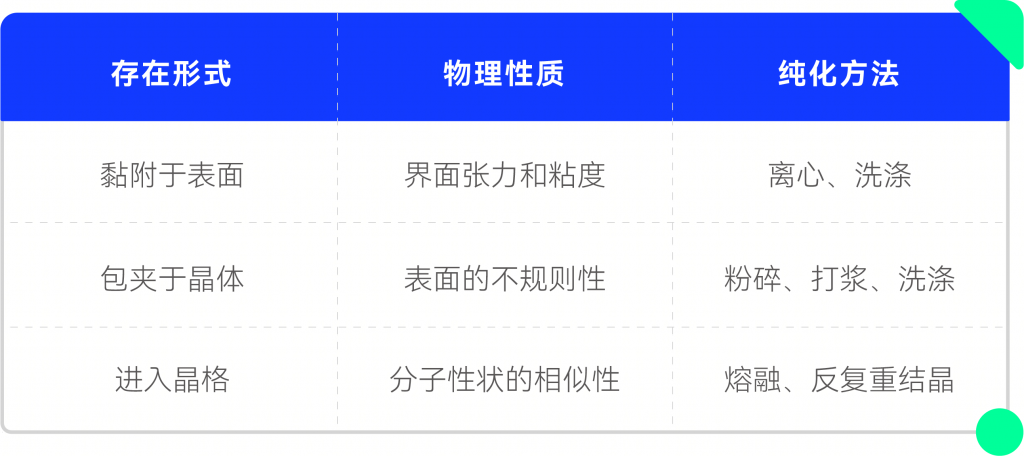
晶体形貌(形状)控制:
晶体的形状取决于晶体表面的相对生长速率。表面生长速度主要是受杂质、添加剂以及溶剂的影响。不同晶体形貌会影响后处理过程(分离、干燥、粉碎),API- 辅料相互作用,溶解速率等方面。
晶体形状控制一般通过控制操作条件,比如控制结晶过程不同过饱和状态,不同混合强度,调整结晶相关参数如温度、升降温速度、正反溶剂滴加速度等来实现,其次还有加入添加剂如表面活性剂、杂质、金属离子等也可对晶体形貌进行控制。
结晶方式选择
制药行业常用的结晶方式主要包括冷却结晶、溶析结晶、反应结晶、蒸发结晶等。其它结晶技术:等电点结晶,适用于氨基酸类结晶;熔融结晶、升华结晶适用于低熔点化合物,常用于晶型筛选过程;超声结晶常用于制备特殊晶种。
结晶方式选择及适用性见下表,结晶方式选择决策树见图 3.
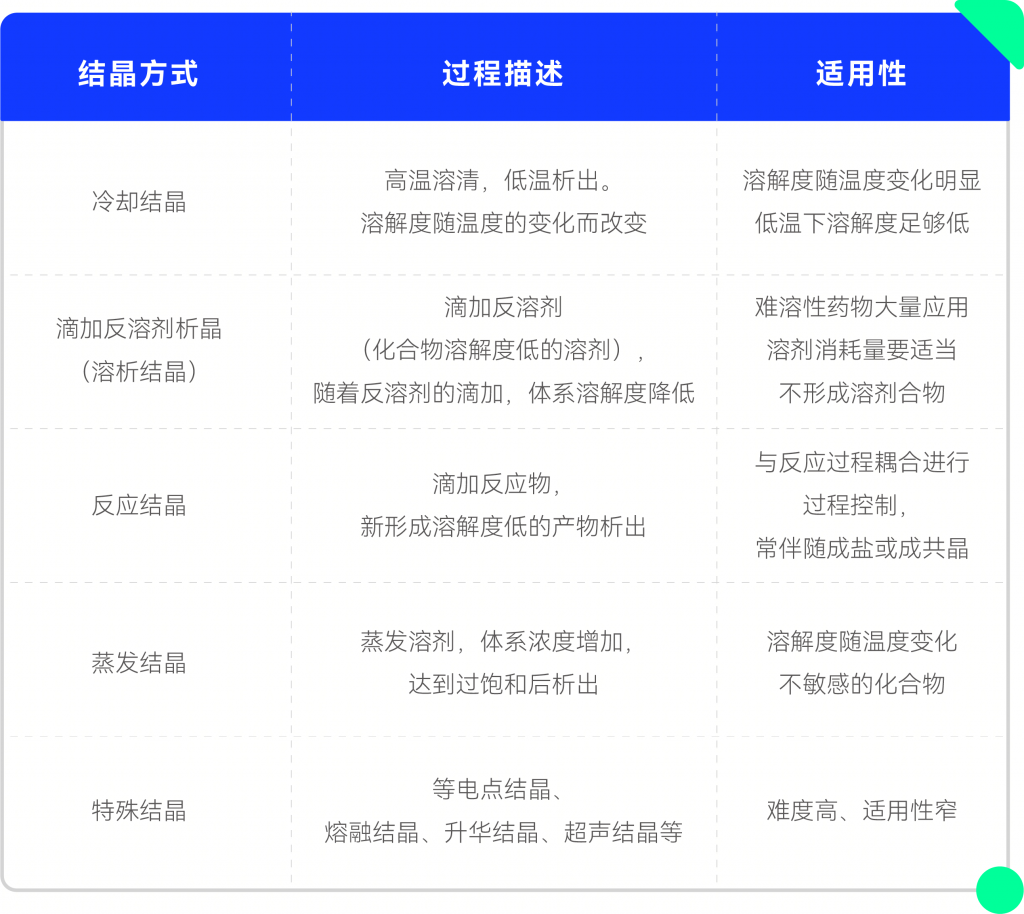
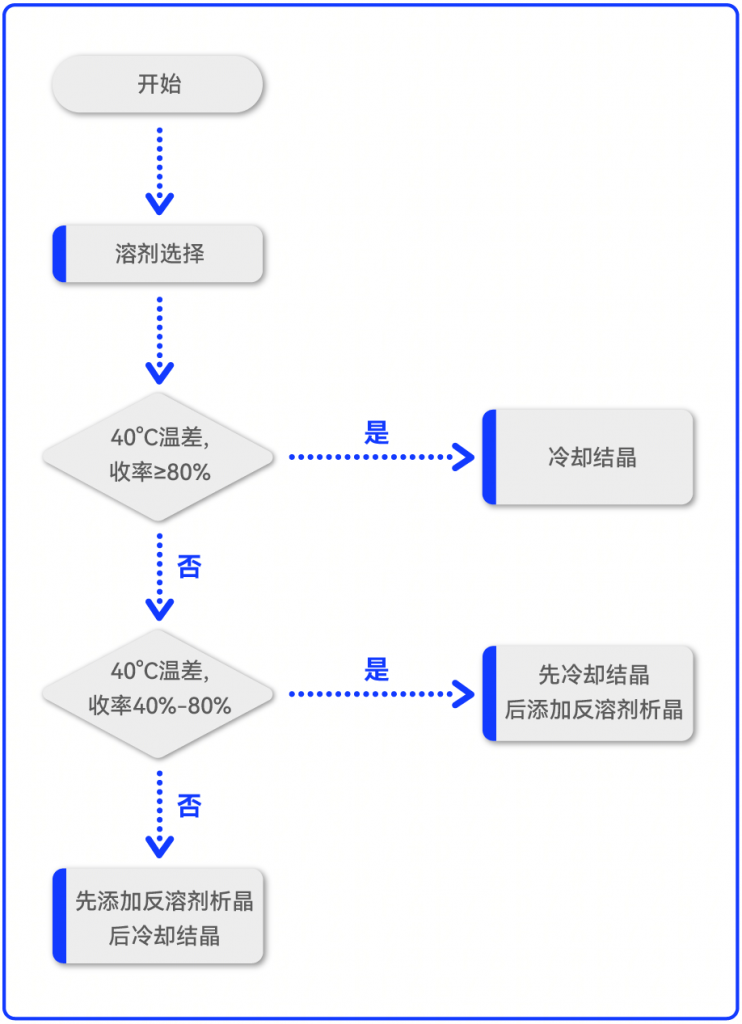
结晶工艺开发常见问题
• 晶体学机理的缺失——对晶体的成核、生长、过饱和度控制缺少一定的认知,导致开发过程中的工艺参数设定盲目、不合理。
• 选择错误的结晶方式——炫技般的选择蒸发结晶、固-固转晶等,导致产品质量差、工艺稳定性差。
• 放大效应研究不充分——对热量、动量、质量的传递研究不充分,导致放大过程中频频出现各种问题。
• 忽视后处理过程——对过滤、干燥方式等研究不充分,导致批量放大后纯度不合格、劳动工时增加等。
• 多晶型研究不充分——对于多晶型尤其是水合物、溶剂合物研究不充分,不清楚各晶型间的热力学互变关系,导致生产过程中出现多晶型问题。
• 未建立收率与纯化之间的关系——收率大小与纯化程度呈相悖的关系,要在满足产品纯度要求的基础上,尽可能的达到收率最大化。
• 缺少结晶过程监测——应用在线、离线设备对晶体生长过程、老化过程进行实时监测,以确定最佳工艺参数。
• 忽视产品理化性质对下游工艺的影响——对粒度、粒度分布、比表面积等粉体学性质充分研究,以达到提高药效和生物活性的目的。
作者介绍:宫正,海思科药业固态研发负责人,具有十余年结晶工艺开发及生产经验,曾就职于豪森药业、科伦药业等国内知名医药企业。